top of page

Engineering Machine Tool Accuracy
Machine Calibrations, Certifications, Analysis
Call Now: 860-837-3172
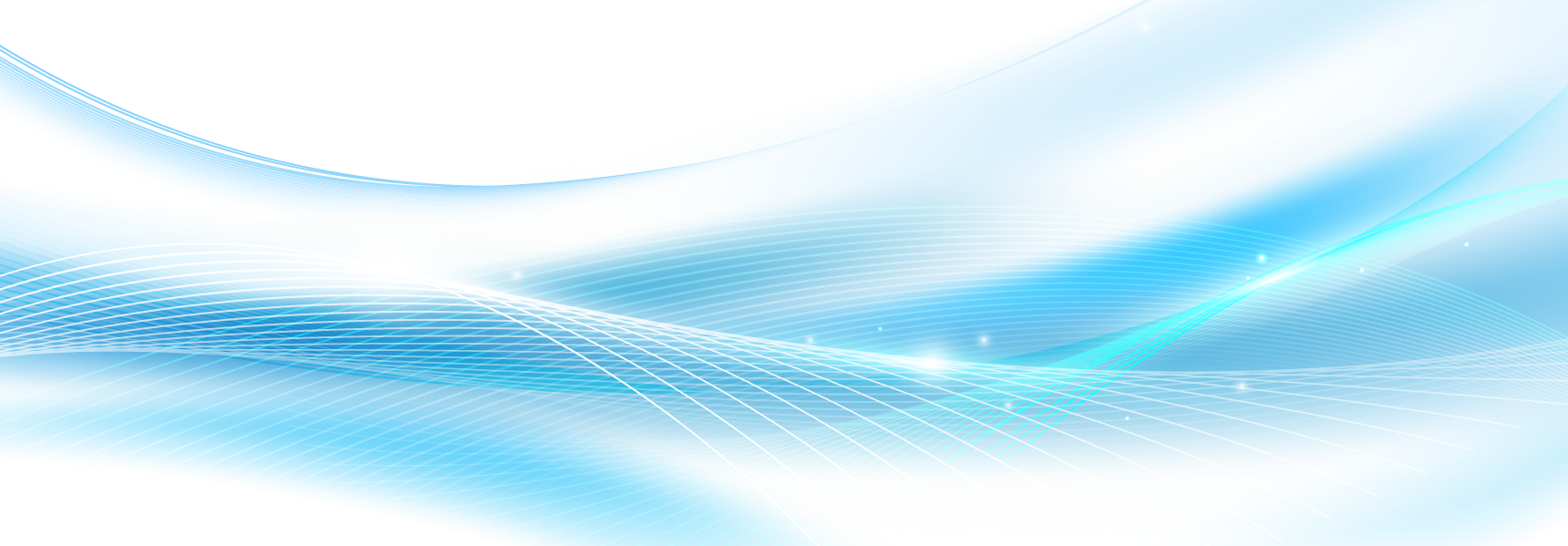



PIONEERING THE FUTURE
OF
MACHINE TOOL QUALITY CONTROL
-
The Phalanx System is a patent pending technological innovation for machine tool geometry error monitoring and management.
-
The System uses an array of proprietary, high resolution precision sensors that are affixed to the machine tool structures, to continuously measure and map the machine tool error changes continuously.
-
The purpose of the system is to maximize productivity on all recipient machines plant-wide by encouraging the use of automatic machine geometry data during the manufacturing process. The use of this data will drive the increase in throughput of quality parts and minimize machine down times.
-
We believe this revolutionary technology will become the industry standard in maximizing quality machine performance and maintenance efficiency.
HOW THE SYSTEM WORKS
The Systems use geometric, accuracy, and volumetric data that was taken prior to installation of the sensors. This is known as the characterization event, where the machine tool is measured and calibrated via traditional methods per ASME B5.54 and ISO 230 standards. The mounted sensors are affixed to the machine to look for change and update the machine geometry error profiles that were taken during the characterization event and are stored in the Phalanx System software algorithms specific to the machine tool. The System computes the following machine tool geometry errors using the updating method:
1. Axis Roll, Pitch, Yaw
2. Axis vertical straightness, horizontal straightness
3. Axis accuracy
4. Volumetric Accuracy
The highlights of the System are:
-
Save time in determining if the machine is suitable for use after catastrophic events
-
Identify, configure, and implement an unlimited number of benchmark locations
-
Set ranges and tolerances for acceptable geometry results
-
Evaluate results via automatic and intuitive gauges and plots at the user interface
-
Trend data by extracting a history of results from the archived results
-
Implement seamlessly and daily as a machine check event that takes just minutes
PHALANX CUSTOMIZED SOFTWARE UI

PHALANX CUSTOMIZED ANALYSES UI
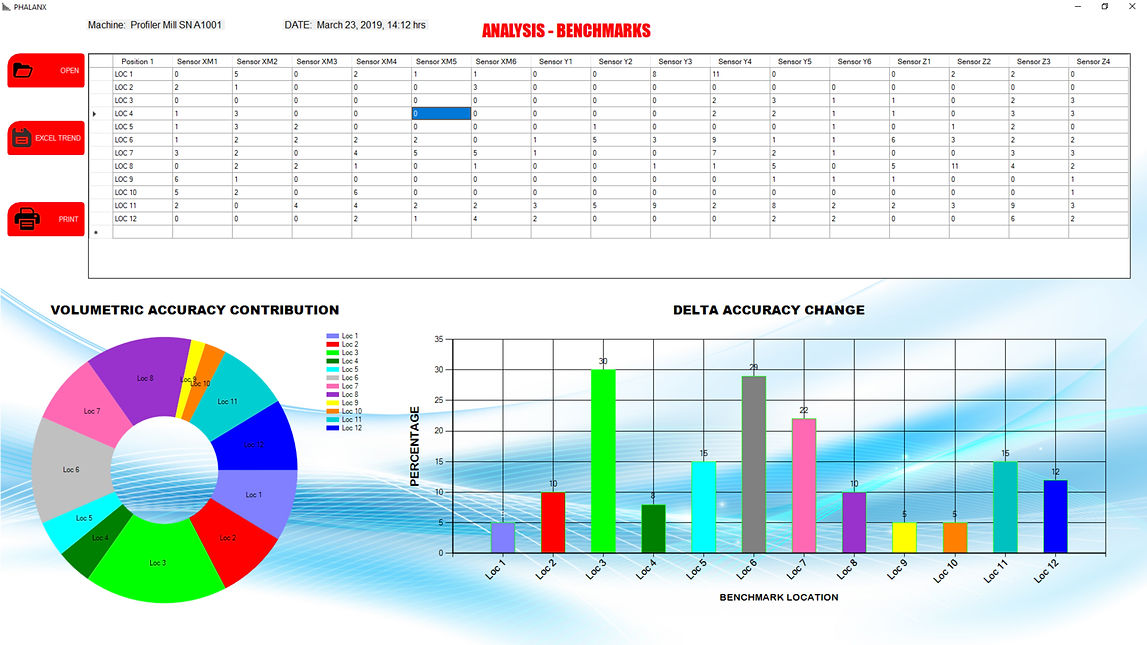
PHALANX SYSTEM BENEFITS
PRODUCTION DEPARTMENT
-
Confidence that the machine is in optimal condition to produce parts within tolerance.
-
For better quality control, the System can be integrated as a machine calibration routine during the manufacturing process.
-
Instant recognition of the machine accuracy performance is utilized to make proactive manufacturing decisions to maintain part quality.
-
Versatility in critical machining decisions driven by machine geometry behavior data
-
In the event of unplanned catastrophic events, the machine alignment status from the System determines if intervention is necessary.
MAINTENANCE DEPARTMENT
-
The machine geometry outputs are straightforward which allow for more time fixing and less time diagnosing.
-
Understand normal machine geometry and accuracy behavior over extended periods of time
-
Evaluate the entire machine geometry data concurrently in order to develop the best plan and execute the decisions for correction.
-
Configure the system by setting allowable machine geometry errors
-
Drive machine alignment events with machine geometry data versus scheduling it on a timed basis.
CONTACT US TO LEARN MORE ABOUT A FACTORY WIDE TAILORED SOLUTION
INFORMATION DOWNLOAD
bottom of page